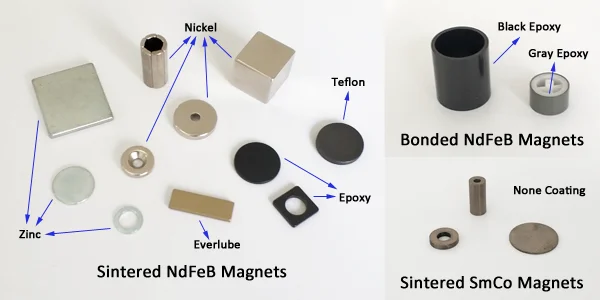
Corrosion Resistance of Rare Earth Permanent Magnets
In the Rare Earth Permanent Magnets family, the 1st generation 1:5 type SmCo magnets and 2nd generation 2:17 type SmCo magnets have high corrosion resistance due to the high cobalt content. Just like ferrite/ceramic magnets and AlNiCo magnets, SmCo magnets usually do not need any treatment for applications. The 3rd generation NdFeB magnets, however, are not the same. Although they have superior magnetic properties, they are more vulnerable to corrosion in humid environments, resulting in the deterioration of magnetic properties and eventual disintegration and failure.
So what is the corrosion mechanism of NdFeB magnets? Generally it is an inter-granular corrosion evolution process. When viewed at the microstructure and microchemistry level, NdFeB magnets mainly consist of two phases:
1. Ferromagnetic Nd2Fe14B grain phase, and
2. Non-ferromagnetic Nd-rich grain boundary phase.
Nd-rich grain boundary phase is so highly reactive that the preferential oxidation occurs when it is exposed to humid environments. As the oxidation progresses, Nd2Fe14B grains loosen, detach and will eventually lead to magnet failure.
Such being the case, NdFeB magnets can be protected from corrosion by the following two directions:
On the one hand, additives (Al, Cu, Dy, Co, Nb, Zr, Mo, Ti, etc.) can improve the corrosion resistance of the magnets themselves to some extent but cause some magnetic properties decrease.
On the other hand, surface treatment/coating is a more effective method to insulate against humid environments. For sintered NdFeB magnets, electroplated zinc and nickel are the most common coatings. Besides, epoxy, Teflon (food grade coating), Everlube and other coatings are also available. In comparison, bonded NdFeB magnets have better corrosion resistance due to resin binders, electrophoretic epoxy is the most common coating for them.
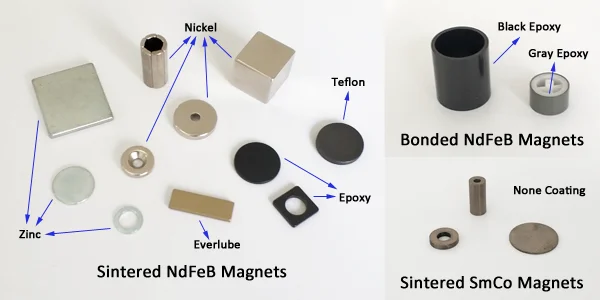
Hi I’m after 4 rare earth disc magnets roughly 25mm by 8mm coated with Teflon for food grade
Would you have anything like this ?
Yours sincerely Rod Rusling
Hi Rod,
Thanks for your visit. I will forward your message to our sales team soon.
Best regards,
HGT Advanced Magnets Co.,Ltd/Technical Support Team